TM 9-2320-387-24-2
33-7. RIVET REPLACEMENT (Contd)
g. Blind Rivet Installation.
1.
2.
3.
4.
NOTE
l Prior to installing blind rivets, the hole must be prepared, and the
parts aligned and clamped firmly in place. These steps are the
same as for solid riveting operations (refer to para. 33-5.d). Proper
drill sizes for standard and oversized blind rivets are given in table
33-2. Countersinking dimensions and minimum sheet gauge for
countersunk blind rivets are shown in tables 33-3 and 33-4.
l It is very important that the proper length rivet is selected for each
application. Rivet lengths are sized by the range of material thickness
that the rivet will grip. Selecting the proper rivet length is critical
because rivets can tolerate only l/16%. variation in material thick-
ness for each particular rivet length Rivet grip lengths are called out
as a dash number at the end of the manufacturers part number. Grip
lengths are determined as shown in appendix F, table F-1.
l For double-dimpled sheets, add countersunk head height to
material thickness.
l Use rivet installation tool kit, D-lOO-ML1, and puller head
adapters, if required, for all blind rivets.
Insert rivet stem into pulling head of rivet gun or adapter.
Hold rivet gun in line with axis of rivet as accurately as possible.
Apply a steady, firm pressure against rivet head.
Squeeze handles of manual gun. The rivet clamping action will pull sheets together, seat rivet head,
and break stem flush with head of rivet.
33-8. ALUMINUM REPAIR
CAUTION
Repairs should not be made on the body using welding or heat for
forming. Heat will only weaken material and cause further
problems.
a Mate&L
Aluminum material used for repair should be of the same alloy and temper as original, if
possible. In general, 6061-T6 aluminum alloy should be used. Material thickness must be the same or thicker.
This alloy will work well for flat repairs, but is not well suited to bending because it is quite hard and cracks
easily when bent sharply. When bends must be made, use softer 6061-T4 aluminum alloy and increase
material thickness by at least 50 percent. As a general rule of thumb, 6061-T4 alloy should be bent with a
minimum bend radius of one to two times material thickness, whereas 6061-T6 alloy requires at least three
times material thickness radius for bends. In all cases, bends should be closely inspected for cracks. A
suitable method for avoiding cracks during bending is to obtain angles that are extruded from 6061-T6 alloy
or use preformed angles for repairs. Bulk aluminum is identified in appendix F, table F-2.
b. Epoxy Adhesive. Where it is necessary to remove parts, note that epoxy adhesive is used in joints.
Use care in parts removal to avoid unnecessary distortion. Parts should be separated by peeling them apart
using a knife or chisel to start the peeling action. Before parts are reassembled, it will be necessary to
remove any remaining cured epoxy from joints so parts will fit together with good, even contact. Use of
epoxy requires special storage and application procedures which do not lend themselves to field repairs. For
this reason, epoxy will not be used for repair. To compensate for the lack of epoxy, additional rivets should be
used when making repairs to existing joints.
33-10
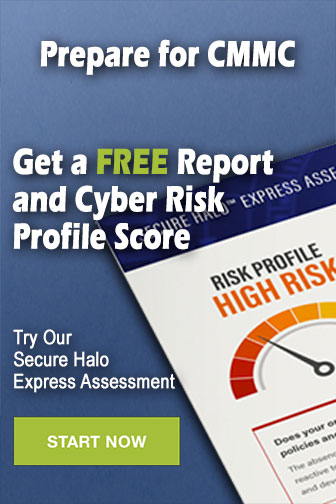