TM 9-2320-387-24-2
33-7. RIVET REPLACEMENT (Contd) 1
e. Hole Countersinking.
NOTE
Some rivet installations in the body require that rivet head be
flush with the material surface. In these instances, countersunk
or flush-head rivets are used.
1. When using countersunk rivets, rivet holes must be countersunk with a tool having a 100 taper so
rivet head will fit flush with surface.
2. When using a hand-operated countersink, the hole must be tried with a rivet so the recess will not
be too deep or too shallow. It is best to use a countersink with a stop on it so depth of countersink can be
controlled. Typical countersinking dimensions for blind rivets are shown in table 33-3. The minimum sheet
thickness that can be machined for 100 countersink rivets is given in table 33-4.
3. Do not remove edge of hole on blind side of joint.
Table 33-3.
Countersinking
Dimensions
for
100 Countersunk
Blind Rivets.
COUNTERSINKING DIMENSIONS (1 DOD)
4-e C
_
OIOR
MIN.
RlVEl
C (INCH)
DIAMETER
(INCH)
MINIMUM
MAXIMUM
1/8
0.222
0.228
!Y32
0.283
0.289
3l16
0.350
0.356
Table 33-4. Minimum
Sheet Gauge for 100 Machine Countersink.
1 RlVET SIZE [INCH1 1 3132
If8
5132
3/16
I/4
1
I- GAUGE (INCH)
1
6.040
0.050
-0.064
0.072
0.072
1
f. Blind Rivet Driving Practices and Precautions.
1. Rivets should be inspected for proper installation. The grip length of each rivet is marked on top of
its head to provide positive identification. Use of proper grip length will produce a rivet installation where
locking collar is flush with top surface of rivet head. Tolerance limit on flushness is 0.020 in. (0.5 mm).
2. For proper rivet installation, it is imperative that holes be properly prepared, tools be in good working
order, and rivets properly applied. When problems occur, the source of trouble could be in any of these areas.
33-9
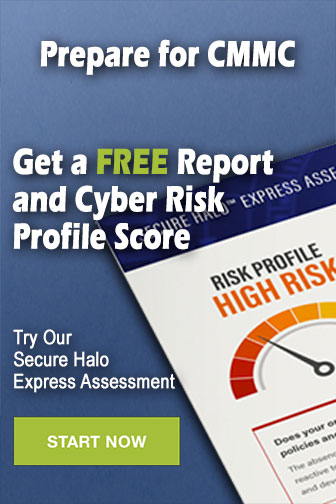