TM 9-2330-392-14&P
5-16
Change 2
5-5
CARGO BODY REPAIR.
This task covers:
Aluminum repair of neglible damage, by patching and by insertion
Initial Setup:
Equipment Conditions:
Parked on level surface.
Wheels chocked (para 2-8.1).
Handbrakes applied.
Materials/Parts:
Rivets
Tools/Test Equipment:
General mechanics tool kit Locknut
Common No. 1 shop set
CAUTION
Repairs should not be made on the body using welding or heat for forming. Heat will only weaken
material and cause further problems.
a.
MATERIAL
1.
Aluminum material used for repair should be of the same alloy and temper as original, if possible. In general,
6061-T6 aluminum alloy should be used. Material thickness must be the same or thicker. This alloy will work
well with flat repairs, but is not well suited to bending because it is quite hard and cracks easily when bent
sharply.
2.
When bends must be made, use softer 6061-T4 aluminum alloy and increase material thickness by at least 50
percent. As a general rule, 6061-T4 alloy should be bent with a minimum bend radius of one to two times mate-
rial thickness, whereas 6061-T6 alloy requires at least three times material thickness radius for bends.
3.
In all cases, bends should be closely inspected for cracks. A suitable method for avoiding cracks during bending
is to obtain angles that are extruded from 6061-T6 alloy or use preformed angles for repairs.
b.
EPOXY ADHESIVE
Where it is necessary to remove parts, note that epoxy adhesive is used in joints. Use care in parts removal to avoid unneces-
sary distortion. Parts should be separated by peeling them apart, using a knife or chisel to start the peeling action. Before parts
are reassembled, it will be necessary to remove any remaining cured epoxy from joints so parts will fit together with good,
even contact. Use of epoxy requires special storage and application procedures that do not lend themselves to field repair. For
this reason, epoxy will not be used for repair. To compensate for the lack of epoxy, additional rivets should be used when mak-
ing repairs to existing joints.
c.
RIVET PATTERNS
1.
Rivet patterns are denoted by rivet spacing and rivet edge distance. Rivet edge distance is the distance from cen-
ter of rivet to nearest edge of sheet. Rivet spacing is defined as the distance from center of rivet to center of adja-
cent rivet.
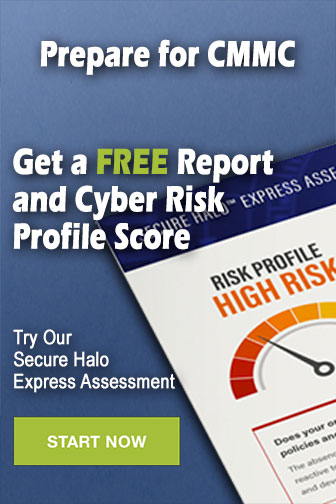